Sistema de barra roscada para sostenimiento del terreno
La barra roscada ha sido fabricado a partir de tubos de acero sin costura de paredes gruesas que cumplen con los estándares API. Estos tubos pasan por un proceso de laminado en caliente para formar las roscas con alta precisión. Las roscas pueden ser del tipo R (redondas), conforme a normas ISO, o del tipo T (trapezoidales), según las especificaciones internas de cada empresa.
El proceso de conformado de la rosca no solo garantiza una alta precisión, sino que además mejora la estructura interna del acero, aumentando la resistencia de la barra de anclaje. Para proteger la barra frente a daños ambientales y la corrosión provocada por el contacto con suelos o rocas, su superficie puede recibir tratamientos como galvanizado por inmersión en caliente o recubrimiento epóxico, asegurando así mayor durabilidad y rendimiento a largo plazo.
El sistema de barra roscada consiste en una barra hueca junto a una broca perforadora compatible, lo que permite realizar la perforación, instalación del anclaje y la inyección de lechada en un solo paso. Este sistema se emplea principalmente en aplicaciones de ingeniería como estabilización de taludes, sostenimiento previo en túneles y refuerzo de micropilotes. Su eficiencia y versatilidad lo han convertido en una solución ampliamente utilizada en sectores como minería, construcción de túneles, ferrocarriles y metro.
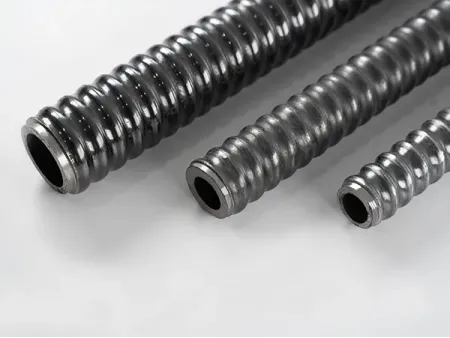
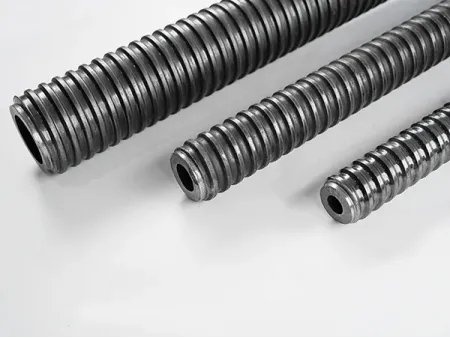
Modelo | Diámetro exterior (mm) | Diámetro interior (mm) | Área de sección transversal efectiva (mm²) | Carga máxima (kN) | Carga de fluencia (kN) | Agt (%) | (kg/metro) | |
R25N-14 | 25.0 | 14.0 | 290 | 200 | 150 | >10% | 2.30 | |
R32L-22 | 32.0 | 22.0 | 350 | 210 | 160 | >10% | 2.80 | |
R32N-21 | 32.0 | 21.0 | 370 | 280 | 230 | >6% | 2.90 | |
R32N-18.5 | 32.0 | 18.5 | 430 | 280 | 230 | >10% | 3.40 | |
R32S-17.5 | 32.0 | 17.5 | 440 | 360 | 280 | >6% | 3.50 | |
R32S-15 | 32.0 | 15.0 | 520 | 360 | 280 | >10% | 4.10 | |
R32SS-14 | 32.0 | 14.0 | 520 | 405 | 350 | >10% | 4.10 | |
R38N-21 | 38.0 | 21.0 | 620 | 500 | 400 | >6% | 4.90 | |
R38N-19 | 38.0 | 19.0 | 700 | 500 | 400 | >10% | 5.50 | |
R38S-18 | 38.0 | 18.0 | 700 | 560 | 460 | >10% | 5.50 | |
R51L-38 | 51.0 | 38.0 | 760 | 550 | 450 | >6% | 6.00 | |
R51L-36 | 51.0 | 36.0 | 970 | 550 | 450 | >10% | 7.60 | |
R51N-36 | 51.0 | 36.0 | 970 | 800 | 630 | >6% | 7.60 | |
R51N-33 | 51.0 | 33.0 | 1070 | 800 | 630 | >10% | 8.40 | |
R51S-30 | 51.0 | 30.0 | 1160 | 930 | 730 | >10% | 9.10 | |
T76N-49 | 76.0 | 49.0 | 2100 | 1600 | 1200 | >6% | 16.5 | |
T76S-45 | 76.0 | 45.0 | 2420 | 1900 | 1500 | >6% | 19.0 | |
T30-11 | 30.0 | 11.0 | 420 | 320 | 260 | >10% | 3.30 | |
T30-14 | 30.0 | 14.0 | 370 | 275 | 220 | >10% | 2.90 | |
T30-16 | 30.0 | 16.0 | 340 | 245 | 190 | >10% | 2.70 | |
T40-16 | 40.0 | 16.0 | 900 | 660 | 525 | >10% | 7.10 | |
T40-20 | 40.0 | 20.0 | 710 | 540 | 425 | >10% | 5.60 | |
T52-26 | 52.0 | 26.0 | 1270 | 930 | 730 | >10% | 10.0 | |
T73-56 | 73.0 | 56.0 | 1380 | 1035 | 830 | >6% | 10.8 | |
T73-53 | 73.0 | 53.0 | 1780 | 1160 | 970 | >6% | 14.0 | |
T73-45 | 73.0 | 45.0 | 2230 | 1600 | 1270 | >6% | 17.5 | |
T73-35 | 73.0 | 35.0 | 2700 | 1865 | 1430 | >6% | 21.2 | |
T103-78 | 103.0 | 78.0 | 3180 | 2270 | 1800 | >6% | 25.0 | |
T103-51 | 103.0 | 51.0 | 5600 | 3660 | 2670 | >6% | 44.0 | |
Dirección de la rosca | Izquierda/ Derecha | |||||||
Normativa de la rosca | ISO 10208 / ISO1720 / otras normas internacionales |
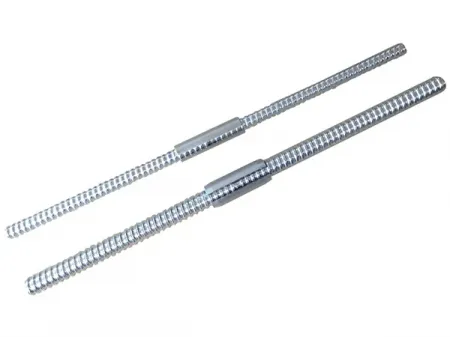
Para reducir la corrosión y prolongar la vida útil de los sistemas de barra roscada, Sinodrills ofrece la opción de galvanizado por inmersión en caliente. Este proceso proporciona una mayor durabilidad y protección frente a los factores ambientales:
Todos los productos galvanizados por inmersión en caliente se fabrican bajo estricto cumplimiento de las siguientes normas, garantizando calidad y rendimiento uniforme:
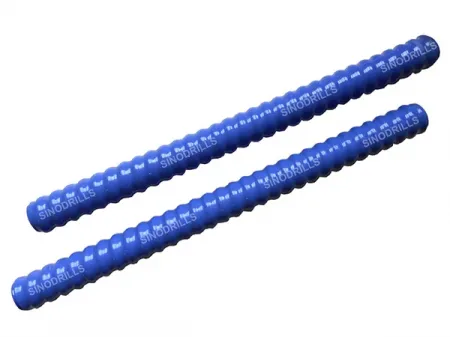
Para proyectos permanentes, especialmente en construcciones subterráneas, es fundamental contar con un sistema de recubrimiento dúplex. Este sistema innovador integra dos capas de protección contra la corrosión: un galvanizado por inmersión en caliente y un recubrimiento epóxico. Esta doble capa ofrece una mayor durabilidad y resistencia frente a la degradación ambiental y química.
El sistema con recubrimiento dúplex está diseñado para cumplir con los estrictos requisitos de los proyectos de ingeniería permanentes y se fabrica en conformidad con las siguientes normas:
- 01Proceso constructivo
Permite realizar la perforación, la inyección de lechada y el anclaje en un solo proceso continuo. La inyección de lechada ocurre de manera simultánea durante la perforación, lo que simplifica la instalación. En cambio, las barras de autoperforante convencionales requieren varias etapas: primero la perforación del agujero, luego la inserción de la barra y finalmente la inyección de la lechada. Esto hace que el proceso sea más largo y requiera mayor mano de obra en el caso de los sistemas convencionales
- 02Adecuación geotécnica
Son ideales para condiciones geológicas complejas, como rocas fracturadas, suelos débiles y arenas sueltas. Su diseño les permite adaptarse a estos entornos difíciles sin afectar su rendimiento. Por otro lado, las barras convencionales suelen presentar problemas como colapsos de perforación o dificultad para formar agujeros estables, lo que genera retrasos y reduce la fiabilidad del sistemaAdecuación geotécnica
- 03Calidad del agujero de perforación
Con las barras autoperforantes, la lechada se inyecta mientras se realiza la perforación, lo que garantiza que las cavidades en las paredes del agujero queden correctamente rellenadas. Esto mejora la calidad del agujero y la estabilidad del anclaje. En el caso de las barras convencionales, la lechada se aplica después de la perforación, lo que puede generar paredes menos estables y un relleno irregular, comprometiendo la integridad del sistema.
- 04Eficiencia constructiva
El método integrado de las barras autoperforantes elimina pasos innecesarios, lo que mejora notablemente la eficiencia y reduce el tiempo de ejecución. Las barras convencionales, por el contrario, requieren un proceso más largo y menos eficiente debido a su método de instalación en varias etapas.Eficiencia en la construcción
- 05Efectividad del anclaje
Las barras autoperforantes permiten una inyección de lechada oportuna y uniforme, creando una mejor adherencia con el suelo y la roca circundante, lo que se traduce en un rendimiento de anclaje superior. En las barras convencionales, la efectividad del anclaje puede ser inconsistente debido a factores como la calidad del agujero y el método de inyección de lechada, lo que genera resultados menos predecibles.
- 06Estructura de barra roscada
Las barras autoperforantes cuentan con una estructura hueca, lo que facilita una inyección de lechada más eficiente y precisa. Las barras convencionales, al ser sólidas, no ofrecen esta ventaja. Por ejemplo, en un proyecto de túnel con condiciones geológicas complejas, las barras convencionales pueden presentar dificultades tanto en la perforación como en la inyección, lo que ralentiza el avance y afecta la calidad del anclaje. En cambio, las barras autoperforantes permiten una formación más rápida del agujero y un rendimiento de anclaje superior, asegurando el éxito del proyecto incluso en condiciones difíciles.Estructura de la barra roscada